Vibration polyurethane shaker screen,sand screen mesh
Benefits of Vibration polyurethane Shaker screens in Oil and Gas Industry Vibration polyurethane shaker screens have become an essential component in the…
Benefits of Vibration polyurethane Shaker screens in Oil and Gas Industry
Vibration polyurethane shaker screens have become an essential component in the oil and gas industry due to their numerous benefits. These screens are designed to efficiently separate solids from drilling fluid, ensuring that the drilling process runs smoothly and effectively. One of the key advantages of vibration polyurethane shaker screens is their durability. Made from high-quality polyurethane material, these screens are able to withstand the harsh conditions of the oil and gas industry, including high temperatures, corrosive fluids, and abrasive materials. In addition to their durability, vibration polyurethane shaker screens are also highly efficient. The vibrating motion of the screens helps to quickly and effectively separate solids from drilling fluid, allowing for faster drilling operations and increased productivity. This efficiency not only saves time and money but also reduces the environmental impact of drilling operations by minimizing the amount of waste generated. Another benefit of vibration polyurethane shaker screens is their versatility. These screens are available in a wide range of sizes and configurations to suit different drilling requirements. Whether you are drilling in shallow or deep wells, in onshore or offshore locations, there is a vibration polyurethane shaker screen that is suitable for your needs. This versatility makes these screens a cost-effective solution for a variety of drilling applications. Furthermore, vibration polyurethane shaker screens are easy to install and maintain. Unlike traditional metal screens, which can be heavy and cumbersome to handle, polyurethane screens are lightweight and flexible, making them easy to transport and install. Additionally, the polyurethane material is resistant to clogging and blinding, reducing the need for frequent cleaning and maintenance. One of the most significant benefits of vibration polyurethane shaker screens is their ability to improve overall drilling performance. By efficiently separating solids from drilling fluid, these screens help to prevent equipment damage, reduce downtime, and improve the quality of the drilling process. This results in higher drilling efficiency, increased well productivity, and ultimately, greater profitability for oil and gas companies. In conclusion, vibration polyurethane shaker screens offer a wide range of benefits for the oil and gas industry. From their durability and efficiency to their versatility and ease of maintenance, these screens are a valuable asset for any drilling operation. By investing in vibration polyurethane shaker screens, oil and gas companies can improve their drilling performance, reduce costs, and minimize their environmental impact. With all of these advantages, it is clear that vibration polyurethane shaker screens are an essential tool for success in the oil and gas industry.Comparing sand screen mesh Materials: Polyurethane vs. Traditional Options
In the realm of sand screening, the choice of materials for shaker screens plays a crucial role in determining efficiency, durability, and overall performance. Among the various options available, polyurethane has emerged as a leading material, often compared to traditional alternatives such as metal and Woven wire mesh. Understanding the differences between these materials is essential for making informed decisions in applications ranging from mining to construction. polyurethane sand screen mesh is renowned for its flexibility and resilience. Unlike traditional metal screens, which can be rigid and prone to wear and tear, polyurethane screens can withstand significant impact and abrasion. This characteristic is particularly advantageous in environments where the material being screened is coarse or contains sharp edges. The inherent elasticity of polyurethane allows it to absorb shocks, reducing the likelihood of damage and extending the lifespan of the screen. Consequently, operators can expect lower replacement costs and less downtime, which translates to increased productivity. In contrast, traditional options such as woven wire mesh, while effective in certain applications, often fall short in terms of durability. Metal screens can suffer from corrosion, especially when exposed to harsh environmental conditions or corrosive materials. This susceptibility not only compromises the integrity of the screen but also necessitates frequent maintenance and replacement. Furthermore, the rigidity of metal screens can lead to issues such as blinding, where particles become trapped in the mesh, hindering the screening process. Polyurethane screens, on the other hand, are less prone to blinding due to their unique design and surface properties, allowing for more efficient material flow and improved screening performance. Another significant advantage of polyurethane sand screen mesh is its lightweight nature. This characteristic facilitates easier installation and handling compared to heavier metal screens. The reduced weight of polyurethane screens allows for simpler integration into existing shaker systems, minimizing the need for extensive modifications. Additionally, the ease of installation can lead to faster turnaround times in operations, further enhancing productivity. In contrast, the heavier weight of traditional metal screens can complicate installation processes and may require additional equipment or labor, increasing operational costs.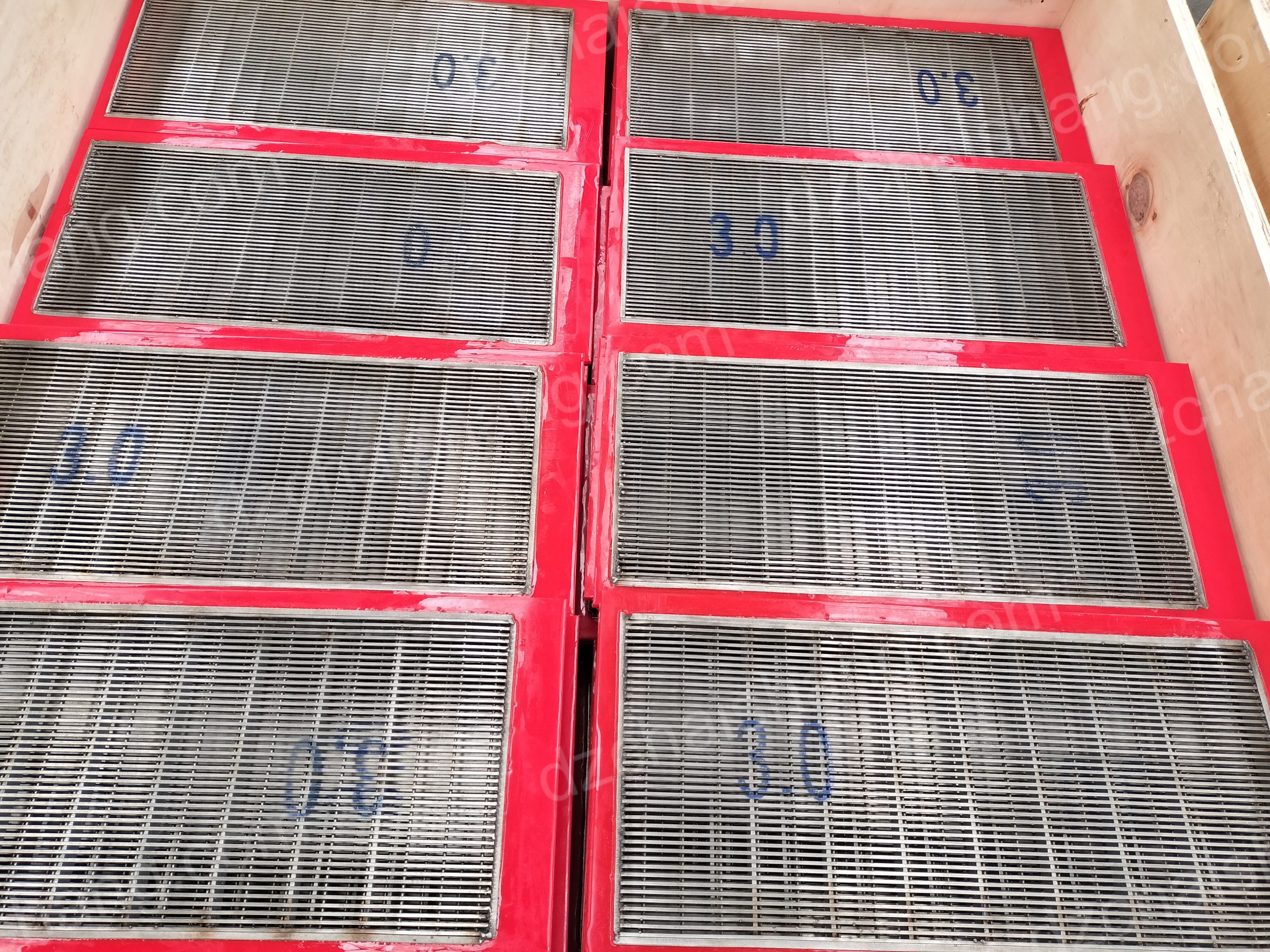
In conclusion, the comparison between polyurethane sand screen mesh and traditional options reveals significant advantages for the former. With its superior durability, flexibility, lightweight nature, and customization potential, polyurethane stands out as a material that enhances operational efficiency and reduces costs. As industries continue to seek innovative solutions for material processing, the adoption of polyurethane screens is likely to grow, reflecting a shift towards more effective and sustainable practices in sand screening applications.