篩板、振動篩網、採石場篩網
在採石場作業中利用先進的螢幕面板技術最大限度地提高效率 振動篩網在物料分選篩分上的演變與應用 篩網技術最重要的進步之一是引入了防堵塞功能。堵塞(顆粒卡在篩孔中)會顯著降低篩選過程的效率。現代篩網透過各種技術來解決這個問題,例如自清潔線,可以振動以清除被捕獲的顆粒,或者俱有錐形開口的篩網,可以防止顆粒滯留。網的一個主要例子是為惡劣的採礦作業條件而設計。這些篩網專為處理大型磨蝕性材料而設計,由重型金屬絲或板製成。採石場篩網的耐用性確保它們可以分選大量的石頭和礦石,而無需頻繁更換,從而減少停機時間和維護成本。聞名。它們不僅限於乾法分選,還可以用於濕式應用。這種靈活性對於選礦等行業至關重要,在這些行業中,材料在分選之前可能需要清潔以去除雜質。例如,在農業中,篩網用於按尺寸分離穀物和種子,確保種植或加工的均勻性。食品業也依賴振動篩對產品進行分類並去除不需要的材料,確保只有最高品質的產品才能到達消費者手中。還遠遠不夠。對新材料和設計的研究有望提供更精緻的解決方案。例如,與傳統金屬絲網相比,聚氨酯篩網的開發提高了耐用性並降低了噪音水平。它從簡單的金屬絲編織到複雜的高性能篩網的演變反映了對材料加工效率和精度的持續追求。隨著技術的進步,我們可以預期振動篩網將繼續在材料的分離和分類中發揮至關重要的作用,從而提高眾多工業製程的生產率和品質。 The Evolution and Applications of vibrating screen mesh in Material Sorting and Sifting The Evolution and Applications of Vibrating…
在採石場作業中利用先進的螢幕面板技術最大限度地提高效率
振動篩網在物料分選篩分上的演變與應用
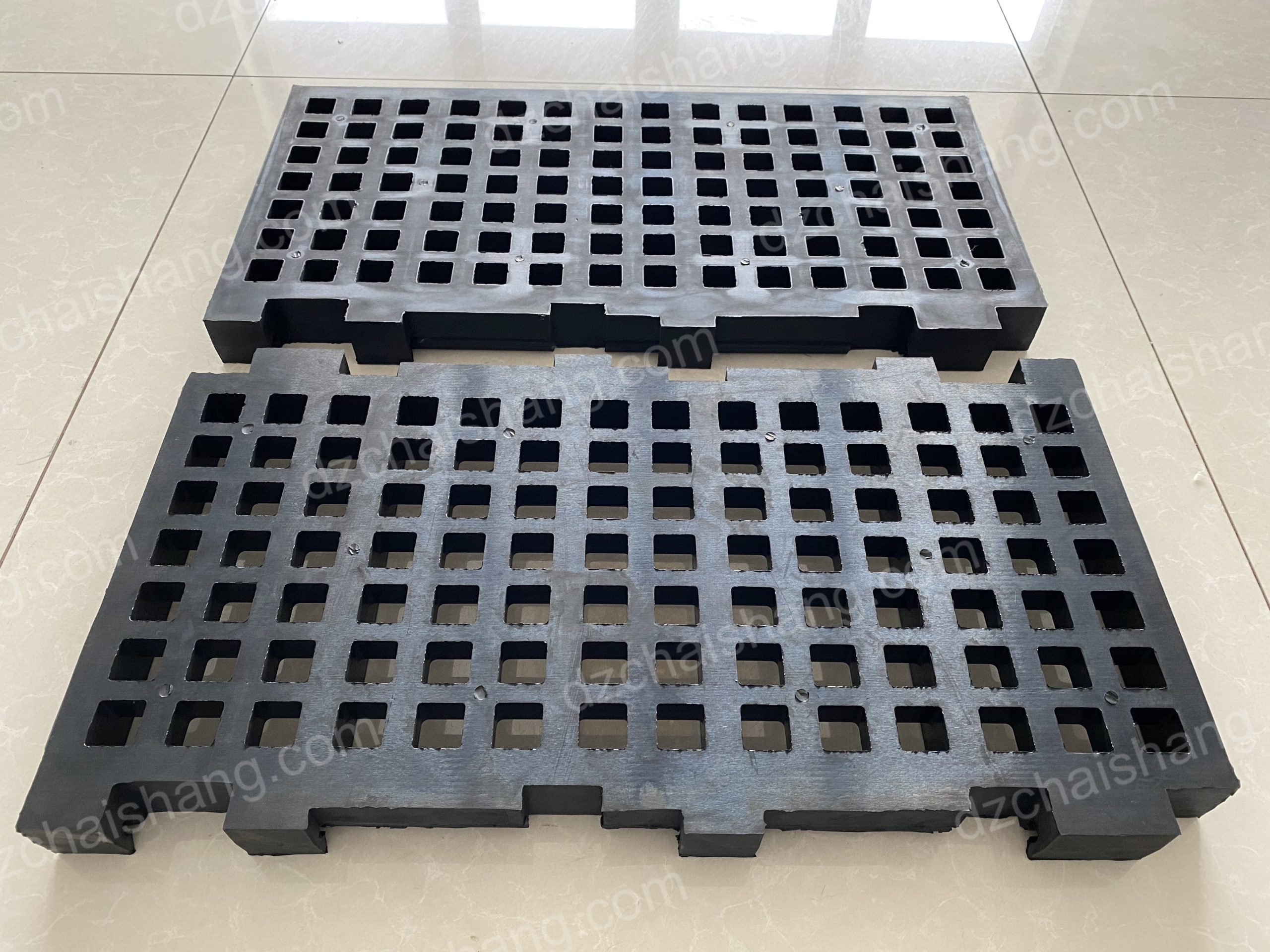
篩網技術最重要的進步之一是引入了防堵塞功能。堵塞(顆粒卡在篩孔中)會顯著降低篩選過程的效率。現代篩網透過各種技術來解決這個問題,例如自清潔線,可以振動以清除被捕獲的顆粒,或者俱有錐形開口的篩網,可以防止顆粒滯留。網的一個主要例子是為惡劣的採礦作業條件而設計。這些篩網專為處理大型磨蝕性材料而設計,由重型金屬絲或板製成。採石場篩網的耐用性確保它們可以分選大量的石頭和礦石,而無需頻繁更換,從而減少停機時間和維護成本。聞名。它們不僅限於乾法分選,還可以用於濕式應用。這種靈活性對於選礦等行業至關重要,在這些行業中,材料在分選之前可能需要清潔以去除雜質。例如,在農業中,篩網用於按尺寸分離穀物和種子,確保種植或加工的均勻性。食品業也依賴振動篩對產品進行分類並去除不需要的材料,確保只有最高品質的產品才能到達消費者手中。還遠遠不夠。對新材料和設計的研究有望提供更精緻的解決方案。例如,與傳統金屬絲網相比,聚氨酯篩網的開發提高了耐用性並降低了噪音水平。它從簡單的金屬絲編織到複雜的高性能篩網的演變反映了對材料加工效率和精度的持續追求。隨著技術的進步,我們可以預期振動篩網將繼續在材料的分離和分類中發揮至關重要的作用,從而提高眾多工業製程的生產率和品質。
The Evolution and Applications of vibrating screen mesh in Material Sorting and Sifting
The Evolution and Applications of Vibrating screen mesh in Material Sorting and Sifting
In the realm of material processing, the ability to sort and sift particulates efficiently is crucial for quality control and preparation for further processing. The vibrating screen mesh, a pivotal component in screening equipment, has undergone significant evolution to meet the demands of various industries, from mining to agriculture. This finely tuned piece of technology not only exemplifies engineering ingenuity but also highlights the importance of adaptation in industrial practices.
Originally, screen panels were rudimentary, often made from woven wire or punched plates that offered basic separation of materials. Over time, as the need for more precise and efficient sorting grew, so did the technology behind screen meshes. Innovations in materials and design have led to the development of screens that are not only more durable but also capable of providing finer, more accurate sifting.
Today’s vibrating screen mesh is a testament to this evolution. Made from high-tensile woven wire or synthetic materials, these meshes are designed to withstand the rigorous conditions of industrial sorting. The wires are woven in a way that creates precise openings, which can be tailored to the specific needs of the material being sorted. This customization allows for the separation of particles by size, shape, and even material type, making the process highly efficient.
One of the most significant advancements in screen mesh technology is the introduction of anti-clogging features. Blinding, where particles get stuck in the mesh openings, can significantly reduce the efficiency of the screening process. Modern meshes combat this with various techniques, such as self-cleaning wires that vibrate to dislodge trapped particles or meshes with tapered openings that prevent particles from becoming lodged in the first place.
The quarry screen mesh is a prime example of a specialized screen designed for the harsh conditions of mining operations. These screens are built to handle large, abrasive materials and are constructed from heavy-duty wire or plates. The durability of quarry screens ensures that they can sort large volumes of stone and mineral ores without frequent replacement, thereby reducing downtime and maintenance costs.
In addition to their robustness, vibrating screen meshes are also celebrated for their versatility. They are not confined to dry sorting but can also be used in wet applications. This flexibility is essential in industries such as mineral processing, where materials may need to be washed to remove impurities before they can be sorted.
The applications of vibrating screen mesh extend beyond mining and industrial uses. In agriculture, for instance, screen meshes are used to separate grains and seeds by size, ensuring uniformity for planting or processing. The food industry also relies on vibrating screens to sort products and remove unwanted material, ensuring that only the highest quality produce reaches the consumer.
As industries continue to demand more precise and efficient material sorting, the evolution of vibrating screen mesh is far from over. Research into new materials and designs promises to deliver even more refined solutions. For instance, the development of polyurethane screens offers increased durability and reduced noise levels compared to traditional wire meshes.
In conclusion, the vibrating screen mesh is a critical component in the sorting and sifting of materials across various industries. Its evolution from simple wire weaves to sophisticated, high-performance screens reflects the ongoing quest for efficiency and precision in material processing. As technology advances, we can expect vibrating screen meshes to continue to play a vital role in the separation and classification of materials, driving productivity and quality in numerous industrial processes.