Mining Processing Screen Mesh,vibrating screen in Mining
Benefits of Using High-Quality mining Processing screen mesh
Mining processing screen mesh plays a crucial role in the mining industry, as it is used in vibrating screens to separate and classify materials. These screens are essential in the processing of minerals, ores, and other materials, as they help to ensure that the desired particle size is achieved. Using high-quality mining processing screen mesh can offer a range of benefits to mining operations, including increased efficiency, reduced downtime, and improved product quality. One of the primary benefits of using high-quality mining processing screen mesh is increased efficiency. These screens are designed to withstand the harsh conditions of mining operations, including high temperatures, abrasive materials, and heavy loads. By using durable screen mesh, mining companies can ensure that their equipment operates at peak performance, resulting in higher throughput and reduced processing times. This increased efficiency can lead to cost savings and improved productivity, making it a worthwhile investment for mining operations of all sizes. In addition to increased efficiency, high-quality mining processing screen mesh can also help to reduce downtime. Downtime in mining operations can be costly, as it can result in lost production and revenue. By using durable screen mesh that is less prone to wear and tear, mining companies can minimize the risk of equipment failure and unplanned maintenance. This can help to keep operations running smoothly and prevent costly delays, ultimately improving the overall profitability of the operation. Another benefit of using high-quality mining processing screen mesh is improved product quality. The quality of the screen mesh directly impacts the quality of the final product, as it determines the size and shape of the particles that are separated. By using high-quality screen mesh that is designed to accurately classify materials, mining companies can ensure that their products meet the desired specifications. This can lead to higher customer satisfaction, increased demand for the product, and ultimately, higher profits for the operation. Furthermore, high-quality mining processing screen mesh can also help to improve safety in mining operations. Vibrating screens are often used in high-risk environments, where workers are exposed to hazards such as noise, dust, and moving parts. By using durable screen mesh that is designed to withstand these conditions, mining companies can help to protect their employees and reduce the risk of accidents and injuries. This can lead to a safer work environment, improved employee morale, and reduced liability for the operation. Overall, the benefits of using high-quality mining processing screen mesh are clear. From increased efficiency and reduced downtime to improved product quality and enhanced safety, investing in durable screen mesh can offer a range of advantages to mining operations. By choosing the right screen mesh for their specific needs, mining companies can optimize their processes, increase profitability, and ensure the long-term success of their operation.How to Properly Maintain and Clean Vibrating Screens in Mining Operations
Mining operations rely heavily on vibrating screens to separate valuable minerals from waste materials. These screens play a crucial role in the processing of ores and minerals, ensuring that the desired product is extracted efficiently. However, like any other equipment, vibrating screens require regular maintenance and cleaning to ensure optimal performance and longevity. One of the most common issues faced by mining operators is the buildup of material on the screen mesh. Over time, particles can become lodged in the openings of the mesh, reducing the efficiency of the screen and affecting the quality of the final product. To prevent this from happening, it is essential to regularly clean the screen mesh to remove any accumulated material. There are several methods that can be used to clean vibrating screens in mining operations. One of the most effective ways is to use a high-pressure water spray to dislodge and remove particles from the mesh. This method is quick and efficient, and can be done without the need for any additional cleaning agents. However, it is important to ensure that the water pressure is not too high, as this can damage the mesh and reduce its effectiveness. Another method that can be used to clean vibrating screens is to use a brush or scraper to manually remove material from the mesh. This method is more labor-intensive than using a water spray, but it can be effective for removing stubborn particles that are difficult to dislodge. It is important to use a soft brush or scraper to avoid damaging the mesh, and to ensure that all material is removed from the screen. In addition to cleaning the screen mesh, it is also important to regularly inspect the screen for any signs of wear or damage. Over time, the constant vibration and movement of the screen can cause the mesh to become worn or torn, reducing its effectiveness. It is important to inspect the mesh regularly and replace any damaged sections to ensure that the screen continues to operate efficiently. Proper maintenance of vibrating screens in mining operations also includes lubricating the bearings and other moving parts of the screen. This helps to reduce friction and wear, prolonging the life of the equipment and ensuring smooth operation. It is important to use the correct type of lubricant for the specific components of the screen, and to follow the manufacturer’s recommendations for lubrication intervals. In conclusion, proper maintenance and cleaning of vibrating screens are essential for ensuring the efficient operation of mining operations. By regularly cleaning the screen mesh, inspecting for wear and damage, and lubricating moving parts, operators can prolong the life of their equipment and ensure that it continues to perform at its best. Taking the time to properly maintain vibrating screens will ultimately save time and money in the long run, as well as improve the overall efficiency of the mining operation.The Importance of Choosing the Right Mesh Size for Optimal Efficiency in Mining Processing Screens
Mining processing screen mesh plays a crucial role in the efficiency and effectiveness of vibrating screens used in the mining industry. These screens are essential for separating and sorting materials during the mining process, and the right mesh size is key to achieving optimal results. In this article, we will discuss the importance of choosing the right mesh size for mining processing screens and how it can impact overall efficiency. When it comes to mining processing screens, the mesh size refers to the number of openings per linear inch in the screen. The size of the mesh openings determines the size of the particles that can pass through the screen. Choosing the right mesh size is essential for ensuring that the screen can effectively separate and classify materials according to their size. One of the main factors to consider when selecting the mesh size for a mining processing screen is the size of the particles being processed. If the mesh size is too small, it can cause the screen to become clogged with material, leading to reduced efficiency and throughput. On the other hand, if the mesh size is too large, it may allow oversized particles to pass through the screen, resulting in poor separation and classification. In addition to particle size, the type of material being processed also plays a role in determining the optimal mesh size for a mining processing screen. Different materials have different properties, such as density and moisture content, which can affect how they behave on a vibrating screen. Choosing the right mesh size based on the material being processed is essential for achieving accurate separation and classification.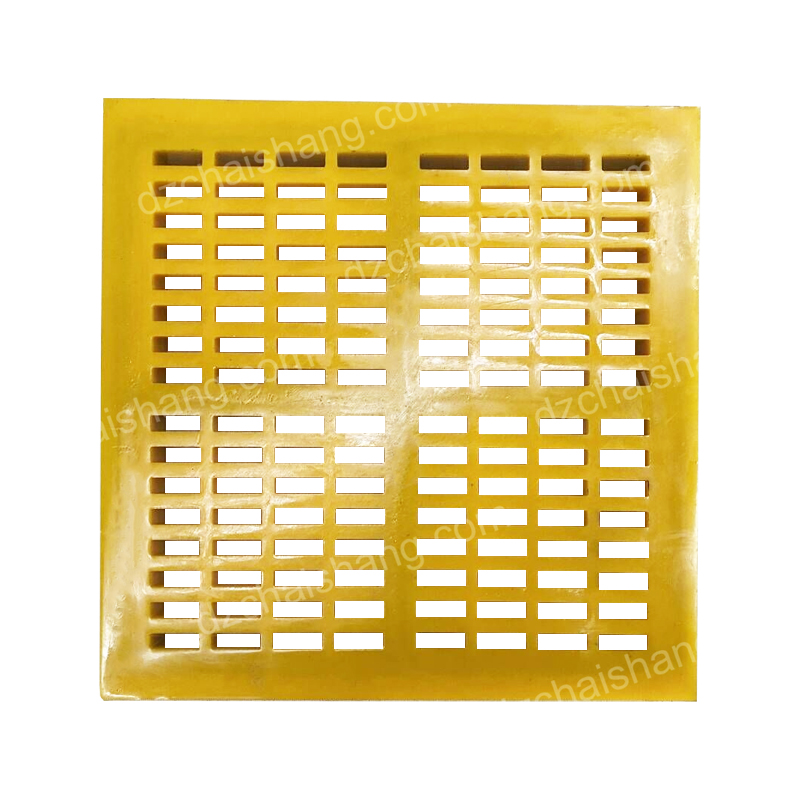
Overall, choosing the right mesh size for mining processing screens is essential for achieving optimal efficiency and effectiveness in the mining process. By considering factors such as particle size, material type, desired output size, and other operating parameters, mining operators can ensure that their screens are able to effectively separate and classify materials according to their size. This, in turn, can lead to increased productivity, reduced downtime, and improved overall performance in mining operations.